Editor’s note: this is the second of a two-part history of the former Loeb-Lorman scrapyard in Fort Atkinson. The story’s first part is found here: https://fortatkinsononline.com/american-tale-immigrants-dream-creates-recycling-history-in-fort/.
By Kim McDarison
The history of the former Loeb-Lorman scrapyard in Fort Atkinson began with the toil and vision of 20th-century emigrants from Russia and continued for more than 100 years as upgrades and expansion led to industrialized mechanization and engagement with foreign markets.
For the scrap industry and Loeb-Lorman Metals, economic decline began with the Great Recession between 2007 and 2009, followed, in 2015, by a petition filed by the company for a state-supervised reorganization, but from 1984 — the year in which Barbara Lorman sold the yard and its assets to the Loeb family of Watertown — to the recession and subsequent reorganization, growth and innovation were the hallmarks of a merged company headed by several generations of two area families.
Serving as an administrative employee for the Loeb family since 1980, Ruth Mack recently remembered much of the scrapyard’s history. As the editor of a company newsletter called “Scraps,” Ruth was able to provide documentation of the scrapyard and metal company’s history spanning some 24 years.
A parallel beginning
Like Louis and Clara Lorman, Ruth said, Hyman Loeb emigrated to American from Russia.
In the early 1920s, Hyman ran a small business from his home in Columbus, Wis. Like Louis Lorman, he began his business with a horse-drawn wagon, going door to door, collecting discarded items such as paper, rubber products, metals and rags. Many of Ruth’s recollections are confirmed by a history provided through the Watertown Historical Society.
At home, the items were sorted and sold for other uses.
Hyman was the father of five sons and one daughter, all of whom helped with the business. He also had help from the community.
According to Ruth, only two of Hyman’s children, William “Bill,” and Archie, made a longterm professional choice to follow their father into the scrap business.
At some point, Ruth said, the family moved to Watertown.
Company documentation notes that Bill and Archie started the Loeb Metal Company in Watertown in 1941 on ground that is today the site of Schurz Elementary School.
By 1951, according to the Watertown Historical Society’s account, Loeb Salvage had moved and was operating from 1111 South Tenth St. in Watertown. The account describes the company as one that used heavy equipment to produce materials that could be sold to refineries and melted into raw materials for new products.
A full accounting from the Watertown Historical Society is found here: http://www.watertownhistory.org/Articles/Loeb_Metal.htm.
Over time, Ruth said, the company grew from Hyman’s humble start as a “junk man” to a salvage dealership and then to an industrialized recycling company.
In 1984, when Barbara Lorman wanted to sell the yard in Fort Atkinson, Ruth said, she wanted to sell to someone who would continue its operation.
Ruth described “a culture of scrap,” saying: “You have to understand the scrap business. It almost has to be in your blood.”
Both the Lorman and Loeb families were well-known in the industry, Ruth said.
“They had already formed a professional relationship and respected one another even before (Barbara’s husband) Milton’s death (in 1979),” she added.
At the time of the purchase, the Lorman scrapyard, with its nine acres, was larger than the 2-acre parcel the Loeb family operated in Watertown.
According to Ruth, family members involved with running the business — along with Hyman, Bill and Archie — included members from the next generation. Bruce Loeb is Bill’s son and Neal Loeb is Archie’s son. The two cousins ultimately took control of the business as partners.
Today, she said, Hyman, Bill, Archie and Neal are deceased.
2L Loeb LLC, the company that recently sold the former Loeb-Lorman scrapyard site to the City of Fort Atkinson, represents the partnership between Bruce and Neal.
When the Loeb family purchased the yard from Barbara Lorman, Ruth said, she believed the Watertown-based Loeb company had about 40 employees, although they did not all work in scrap. Some worked for another branch of the company in refuse collection called Advance Service Corp.
Ruth said the Loeb organization purchased the Lorman property and its tangible assets, including the scrap on the ground and equipment.
After purchasing the yard in Fort Atkinson, Ruth recalled, the company’s roster of employees grew to between 80 and 100.
In the decades that followed, she said, for the Loeb family company, there was a robust period of growth, characterized by expansions made through an increased customer base, including foreign markets, property acquisitions and landfill site development, and efficiency upgrades made at the company’s scrapyards.
Much of that history is documented through “Scraps,” which offers a collection of stories, between 1991 and 2015, of companywide professional and social activities.
‘Scraps,’ the growth years
The 1990s
1991 was described in the newsletters as a good year for the Lorman site, best exemplified in a letter from OLIN company, in East Alton Ill., which read: “congratulations on your performance during the first half of 1991. We appreciate your good performance and thank you for the effort you have made to reduce the reject rate of your deliveries …” According to the newsletter, the Lorman site shipped over 87,000 pounds of metal.
1991 also marked the beginning of construction of the Deer Track Park, Inc., sanitary landfill, located today on Waldmann Lane in Watertown. The company underwent a process called “siting,” which took two years to complete, according to the newsletter. Ruth described the siting process as one where appropriate permits are obtained and a process is undertaken to bring a site into compliance with state Department of Natural Resources (DNR) regulations and requirements. The site is operated today by Texas-based Waste Management Solutions.
Plans, In 1991, called for an anticipated 44-acre landfill to be lined with 60-mil, high-density polyethylene.
“This liner will make our landfill 1,000,000 times safer than an unlined landfill,” the newsletter reported.
In its “Autumn 1991” edition, the newsletter announced the installation of new equipment at the Lorman site, including a $50,000 “metal washer,” used to remove solvents, dirt and foreign materials from ferrous (with iron) and non-ferrous metals. A cleaner product would command higher prices in the marketplace, the newsletter noted.
A second machine, which “flattens and shears non-ferrous metals in one operation” was also installed. The new machine promoted uniformity in the yard’s product and added a component of safety.
Socially, in September of that year, the company held its annual picnic at the Milwaukee County Zoo, where employees and their families were treated to a catered meal.
The “Winter 1991-92” edition announced a change in company leadership: “effective Jan. 1 1992, Archie Loeb “is no longer involved in the direct day-to-day management of the companies, but will direct his time in the purchasing of sales and scrap metal.”
Bruce Loeb officially assumed Archie’s responsibilities pertaining to company management. He would oversee Lorman Iron and Metal, and Loeb Metal. Neal Loeb at that time assumed the responsibilities for directing Advance Service Corp., the garbage collection branch of the company, and Deer Track Park, Inc., the company-owned landfill.
The newsletter also highlighted advancements at the Loeb Metal Recycling plant in Watertown, noting that the company was annually processing over a million tons of product.
In February of 1992, a special edition of the newsletter noted, the company’s board of directors had deemed the Deer Track Park landfill project of “primary emphasis of the organization in both money and time investment.”
Also that year, plans were laid to consolidate the processing of ferrous metals, moving most of that activity to Fort Atkinson.
In the spring of 1992, an update prepared company employees for the opening of Deer Track Park. Construction was completed in December of 1991, and an opening date was under review by the DNR. The landfill was described as having a total of 38 acres, which would be built in seven modules. The total capacity of the full landfill was 3,195,100 cubic yards of refuse. The landfill received its first load on June 18, 1992.
The Winter/Fall 1992-93 edition brought news of another company picnic. Held Sept. 20, 1992 at the Milwaukee County Zoo, the outing was attended by some 200 employees and their guests. As an indicator of company growth, in the fall of 1993, some 300 people attended the company picnic.
Another employee outing hosted by the company occurred on Aug. 22, 1993, when the Carson & Barnes Circus arrived in Watertown. Loeb company employees and their families were treated to the event.
In the summer of 1995, a new custom-built scale was added at the Lorman yard. The new scale and its installation came at a total cost of $40,000.
As part of the new scale, a radiation detector was installed. The improvement was made, according to the newsletter, as “more and more of our foundry customers are requiring the loads to be checked for radiation contamination before they will purchase materials.”
The cost of the detector was estimated at between $35,000 and $38,000.
“Hot” or contaminated items, the newsletter noted, would be rejected and not purchased by Loeb Industries.
“If items are found to be hot, a procedure is in place for disposal of the materials through the State of Wisconsin Radiation Protection Agency,” the newsletter continued.
In 1996, the University of Wisconsin-Whitewater football team, the “Warhawks,” arrived at the Lorman yard for a photo op. The team was calling itself “the wrecking crew,” according to the newsletter, and wanted photographs of its members standing near a pile of iron. Then-coach Robert Berezowitz posed with the team.
In the winter of 1996, a new shear, described as a “gigantic high pressure machine,” was purchased for the Lorman site. The equipment was described as having “a shearing force at the blade of 1,200 ton.”
In 1997, it was reported in the newsletter that William Loeb, at the age of 80, had passed away on Aug. 15.
“Bill’s greatest legacy was, perhaps, his ability to make everyone feel that they were important to him and our company,” the newsletter stated.
Also in 1997, a new quality control system was on its way to yards in Fort Atkinson and Watertown.
“What is ‘ISO 9002’?” a newsletter headline asked. Employees learned that the new system, produced by the International Organization for Standardization (ISO), was being developed for use by companies worldwide. Loeb-Lorman had expanded its clientele and was serving companies worldwide and was therefore adopting the new standards. The company would be among the first, the newsletter stated, adding that the move would help the company satisfy customers by lowering costs through cutting down on waste.
2003 to 2014
In 2003, according to the newsletter, some 145 employees and their families attended the company picnic.
In December of 2003, a new liquid oxygen tank was installed at the Lorman yard. It was installed to reduce the cost of liquid oxygen, according to the newsletter. The new tank could hold 2,500 gallons. The project also included underground piping form the tank to a storage tank at the yard’s torch station.
Also announce in the newsletter, Ruth Mack, the editor of the newsletter, was named 2002 Citizen of the Year by Dodge County Law Enforcement. The Dodge County Sheriff’s Department was able to purchase 11 cameras with money collected through an aluminum can drive, which was conducted by the Beaver Dam Kiwanis Club. Ruth served the club as chairperson.
In 2006, the newsletter reported, changes were made to the ISO system. New safety and environmental rules were added with the adoption of ISO 9001. New policies associated with the change asked employees to adopt what the newsletter described as the “Lorman formula: service, solutions, satisfaction, safety, preventing pollution.”
With new policies and passage of a pending audit, the company would become ISO 9001, ISO 14001 and OHSA (Occupational Safety and Health Administration) 18001 registered.
In 2007, the company announced the completion of a new Reedsburg scrapyard, which offered an opportunity to move scrap by rail from sites in Watertown and Fort Atkinson, where it would be used to supply the Grede Foundry, which, according to the newsletter was one of the Loeb family’s biggest customers.
Bringing the 7-acre site online included purchasing the property, cleanup efforts, and its annexation into the community of Reedsburg.
Also in 2007, the company obtained a license to sell metal to China. The company announced it would seek out opportunities in India as well.
In 2008, in celebration of ISO and OHSA registrations, a dinner was held at Jansen’s Banquet Hall in Fort Atkinson. The dinner was attended by 95 employees and guests. Speakers, including Bruce Loeb, thanked employees for their efforts and stressed the importance of being good stewards of the environment as a component of their work.
During the event, employees were made aware of a correspondence sent by Rob Kantner, described as “a nationally known ISO consultant,” who wrote: “Congratulations to you and the entire Lorman team. Lorman is only the third U.S. scrap recycling firm to implement and certify an integrated quality/environmental/ safety management system. I am grateful for having had the chance to work on it.”
Also in 2008, a report about the year’s community picnic noted some 69 Loeb-Lorman employees and their families attended the event which was held at the Jefferson County fairgrounds. Each employee in attendance received a Loeb-Lorman Metals, Inc., hat and a gift of $300.
‘World economic slowdown’
The newsletter in 2008 delivered news about what it termed “a world economic slowdown.”
Addressing his employees by letter, Bruce Loeb wrote that the slowdown hit the economy “very quickly,” putting management in the position of having to make “hard decisions.”
Bruce looked forward to 2009, hoping government intervention might bring some relief.
He wrote: “We have taken steps to maintain the viability of our company and assure that we are part of the recovery which will surely occur.”
In 2011, a Loeb-Lorman employee, Ernie Heine, was recognized by Fort Atkinson’s Heart of the City organization as its “Big Heart” award recipient. He was chosen for his work as a volunteer at the Fort Atkinson farmers market, the group said.
Also in 2011, the newsletter noted the company’s pride in its relationship with Opportunities, Inc., in Fort Atkinson, adding that together, the two companies had worked on many projects.
“Our company, especially Archie Loeb, was honored by Opportunities at their 45th Anniversary Gala on July 28, 2011. The Commitment Award was given to the Loeb family and Loeb-Lorman Metals for decades of continuous commitment to their organization,” the newsletter announced.
In 2012, a new scale was added in Fort Atkinson at the Petrolane site north of Hake Street. The scale had the ability to be remotely operated from a station at the Lorman Street office.
The newsletter thanked the City of Fort Atkinson for its help in bringing the project to fruition, saying that then-city manager John Wilmet “toured the new scale location and expressed his pleasure with Loeb-Lorman’s efforts to be good neighbors and responsible corporate citizens.”
Also in 2012, a shredder, dubbed “the Little Red Giant,” was installed at the Fort Atkinson yard. The machine could be remotely operated by a single person, the newsletter noted.
In 2014, at the company picnic, which was again held at the Jefferson County fairgrounds, Bruce Loeb thanked his employees for another year of hard work.
According to the newsletter: “(Bruce Loeb) briefly summarized economic conditions affecting the scrap industry and our efforts to improve our production. He highlighted new customers for our products and our plans for the near future.”
At the time, the company purchased a property at 815 Jefferson St. in Fort Atkinson, with plans to convert it into a buying site for over-the-counter customers and providing an access point to facilitate an easier flow of semi traffic in and out of the scrapyard.
The 2014 newsletter was the last included in Ruth’s binder.
2015: Petition for receivership
In 2015, the Loeb-Lorman Metal company petitioned the state, filing in the Jefferson County Circuit Court, for receivership protection.
With company assets listed at $18.2 million and debts totaling $17.2 million, the company applied for a state-supervised reorganization plan which would allow another company to purchase some of its assets and continue their operation. At the time, according to Information included within the Watertown Historical Society’s history, the company owed its largest creditor $10 million.
Falling iron prices and a decreasing demand from foreign markets for raw materials supplied by the company were cited as reasons for its need for restructuring.
The move allowed the company to strategically restructure while continuing the day-to-day operations of its yards.
St. Louis-based Alter Trading Corp purchased the Wisconsin-based assets of Loeb-Lorman Metals, Inc., in 2015. The yards in Fort Atkinson, Watertown and Reedsburg were among assets purchased. The assets were sold by a court-appointed receiver as part of the bankruptcy petition with those monies used to pay company debt.
At the time of the sale, the company was reported having about 70 employees: 20 in Watertown and 50 in Fort Atkinson.
The scrapyard in Fort Atkinson ceased operation after the purchase.
The former Loeb-Lorman yard in Fort Atkinson was recently purchased by the City of Fort Atkinson.
The city extended its offer to purchase the parcels from 2L Loeb LLC in December of last year. The offer came with two components, the first extended to the seller a lump sum of $182,000, with the land’s remaining value, estimated at $550,000, to be used tor site remediation. Any monies not used for remediation will be returned to the seller, according to city documents.
A second phase of work to evaluate the site for contamination is underway. A report of those findings is anticipated in September.
Future plans for the site involve returning it to open or “pad-ready condition,” according to Fort Atkinson City Engineer Andy Selle, after which the site must sit vacant for five years before something new can be established.
What that might be is still under discussion, he said.
A story about the remediation of the land is found here: https://fortatkinsononline.com/city-to-begin-second-phase-remediation-process-at-former-loeb-lorman-site/.
The following photos, unless otherwise indicted, are supplied courtesy of the Loeb family. They depict activity occurring before the company’s Wisconsin properties were sold as part of a 2015 strategic reorganization plan.
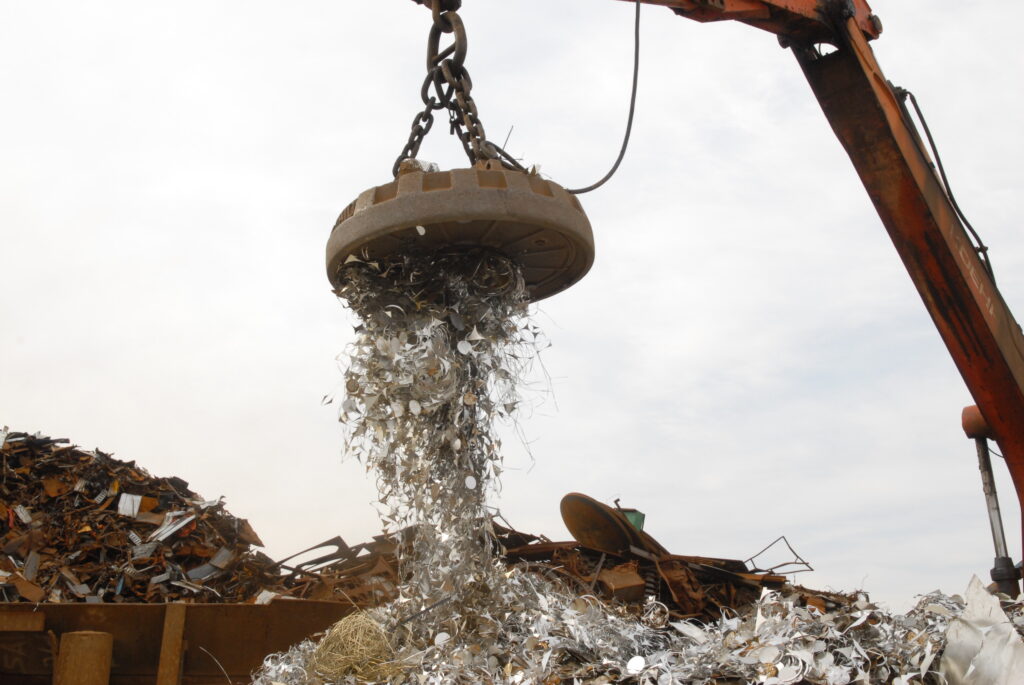
A large magnet is at work lifting and sorting scrap. Pictured is a tin can manufacturer’s scrap which was purchased by Loeb-Lorman Metals. The materials were next sold to a foundry where they would be melted and made ready for use as a manufacturing raw material.
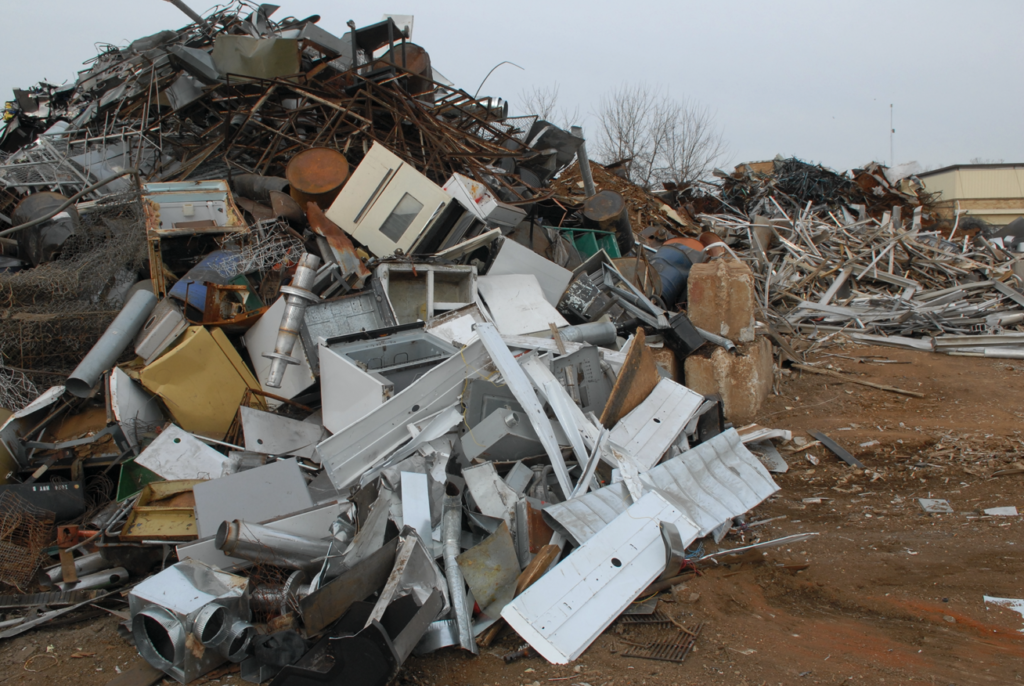
Scrap, waiting to be sorted and cleaned to foundry specifications, is stored at the Lorman yard. Materials like those pictured were typically brought to the yard by members of the public.
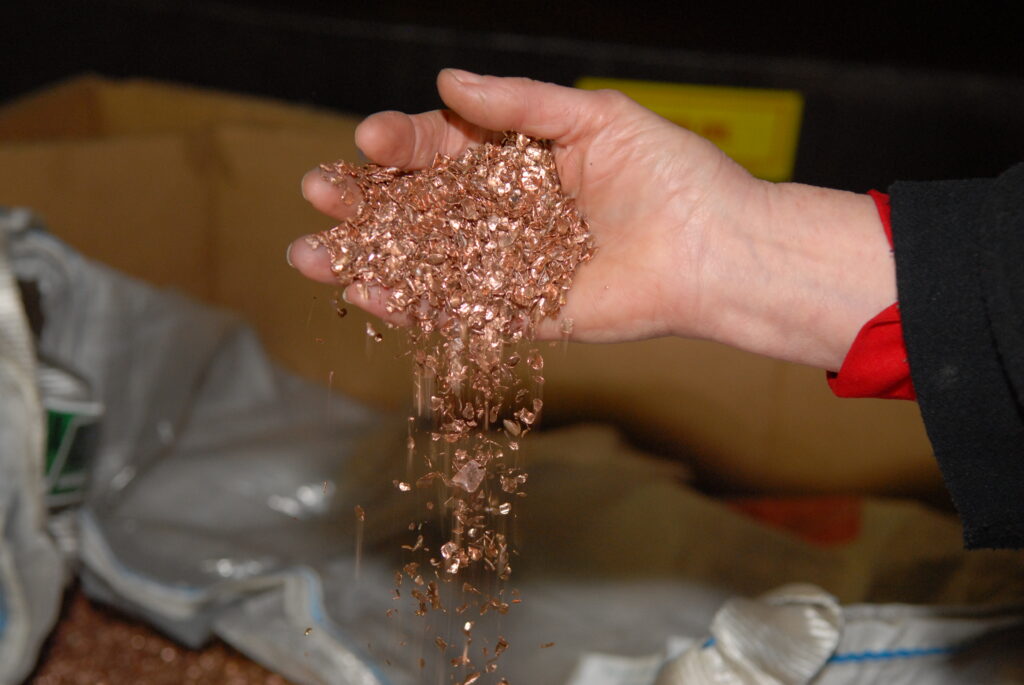
Longtime Loeb family employee Ruth Mack sifts through a handful of copper granules. The foundry-ready material was made by sending copper wire through a “granulator” which would strip plastic and insulation from the wire and chop the remaining copper into confetti-sized pieces.
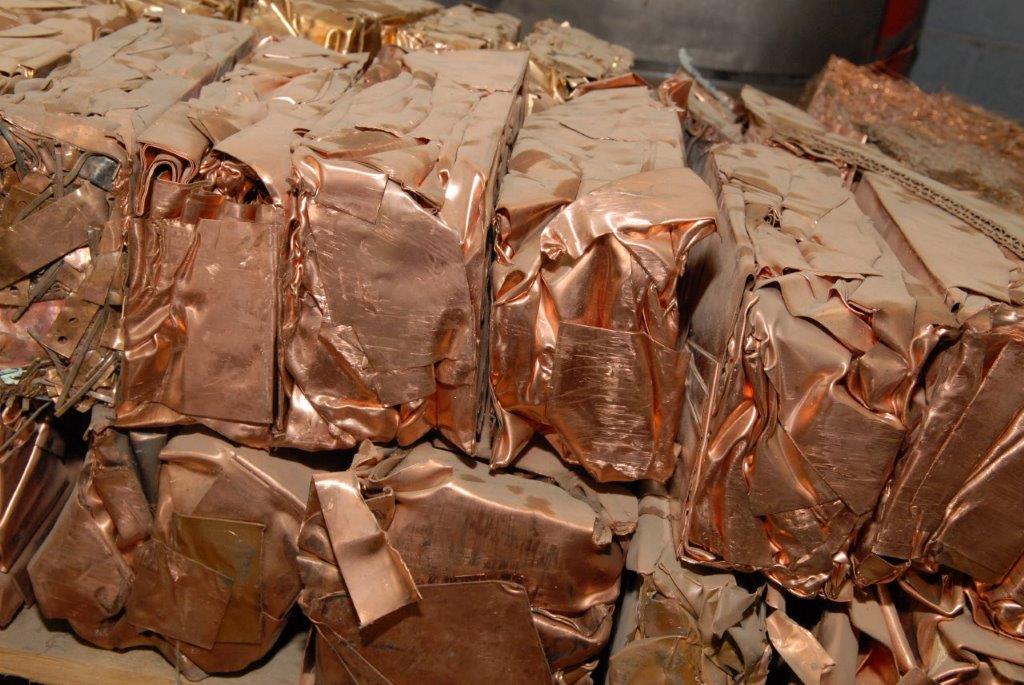
At the yard, copper is compressed into bricks for use at the foundry. The material typically arrived in sheets, longtime Loeb family employee Ruth Mack said.
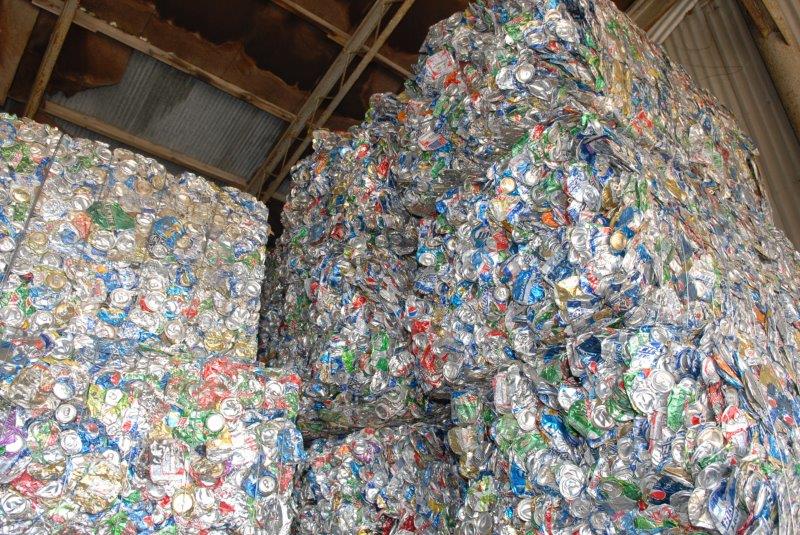
Aluminum cans are baled in anticipation of transport to the foundry.

Loeb-Lorman employees, including foreman Jon Allen, at left, work at a table where they remove unwanted pieces of material from metal scrap that will be sold to a foundry.
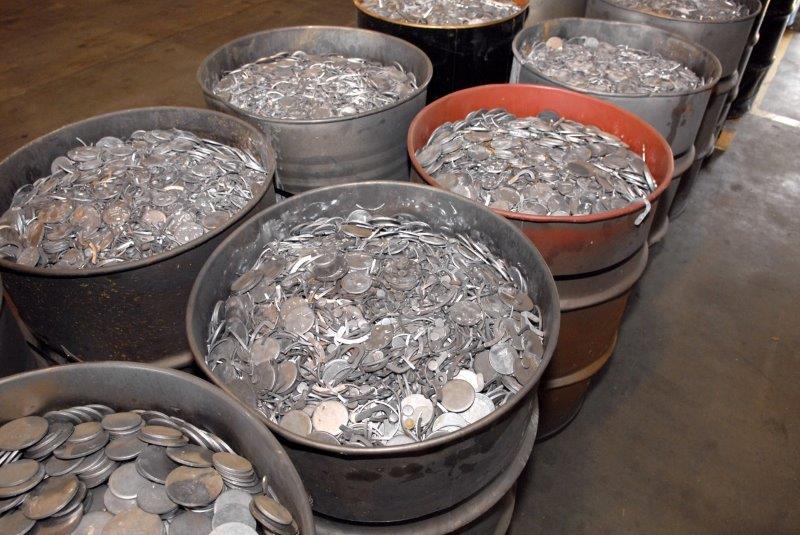
After undergoing a washing and sorting process, these bits of metal, called “punchings,” are placed in barrels and made ready for sale to foundries. Punchings were often a byproduct of the car industry, according to longtime Loeb family employee Ruth Mack.
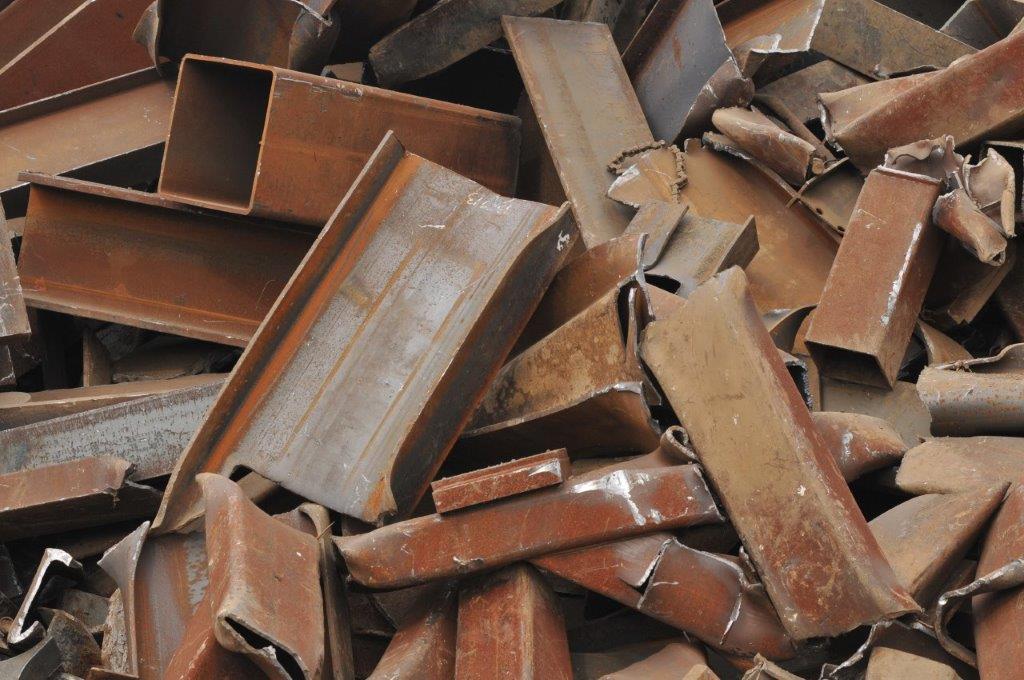
Pictured is iron that has been processed for foundry grade use.
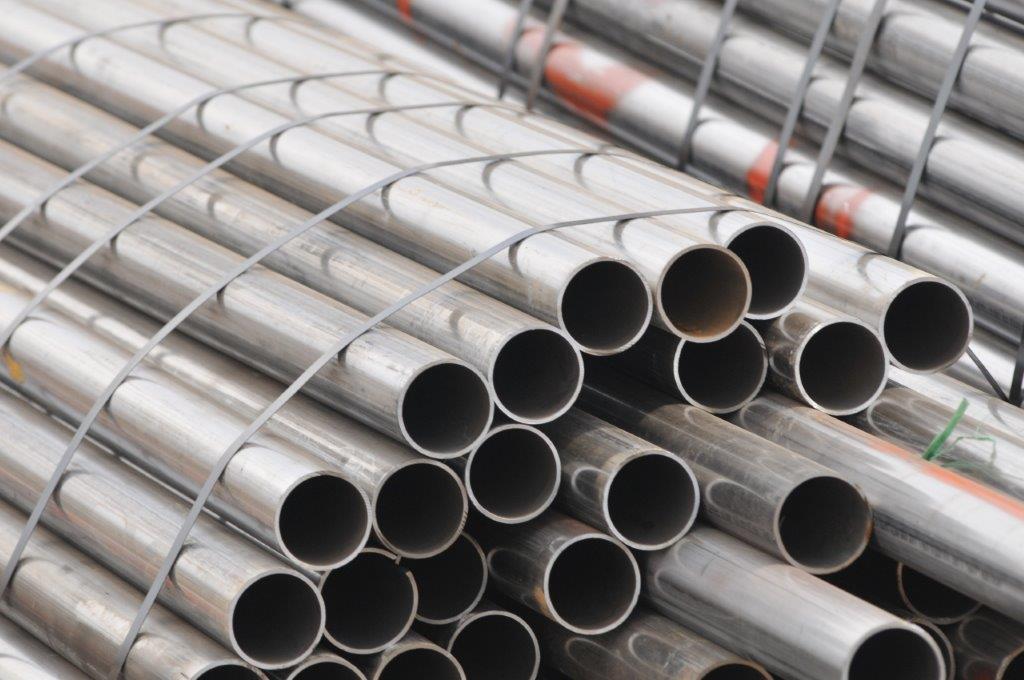
Above: stainless steel scrap arrives in the yard as piping. To process it for foundry use, the piping was cut into six-inch pieces and flattened (pictured below). The materials were cleaned and dried before flattening, and were not completely flattened to make sure no moisture remained before they were introduced into the foundry.
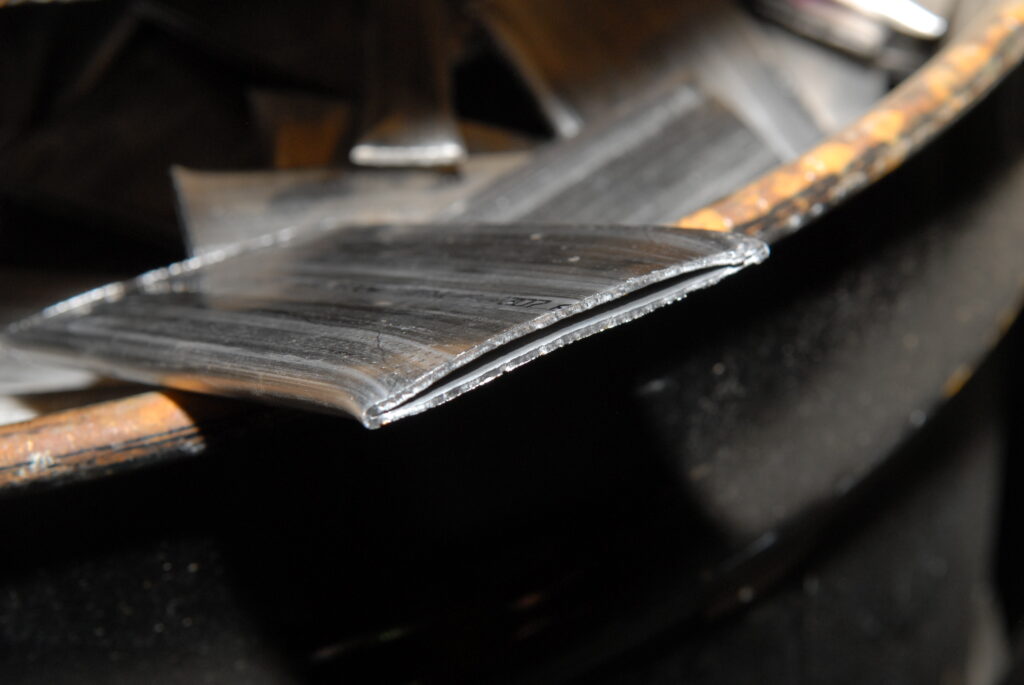
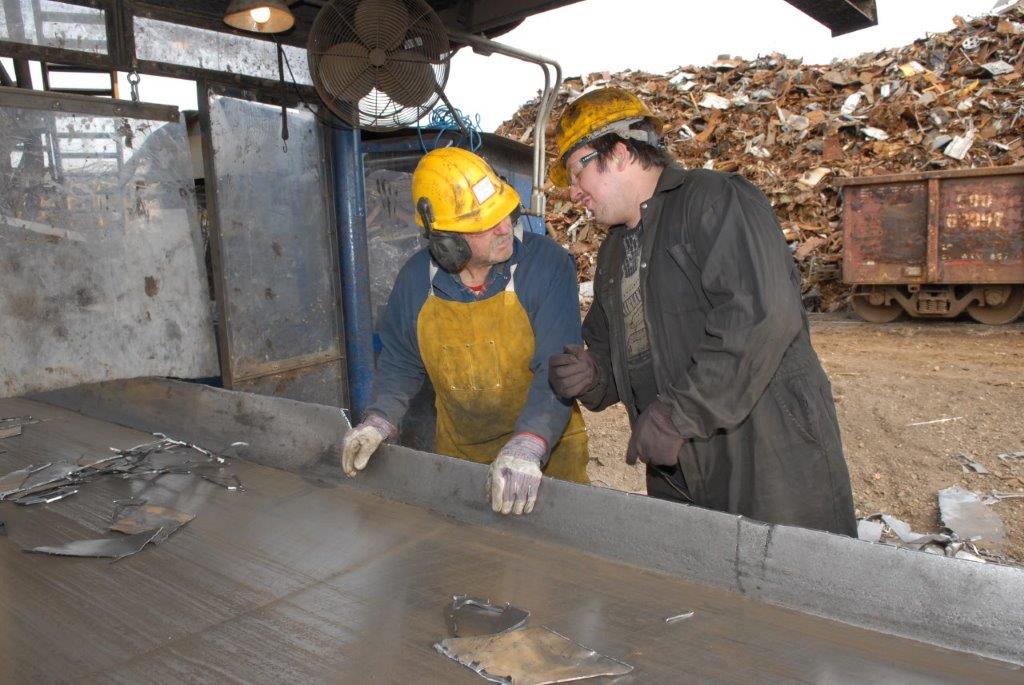
Lorman yard employees perform quality control tasks. The task involved making sure metals met with foundry specifications and unwanted materials were not passed onto the foundries.
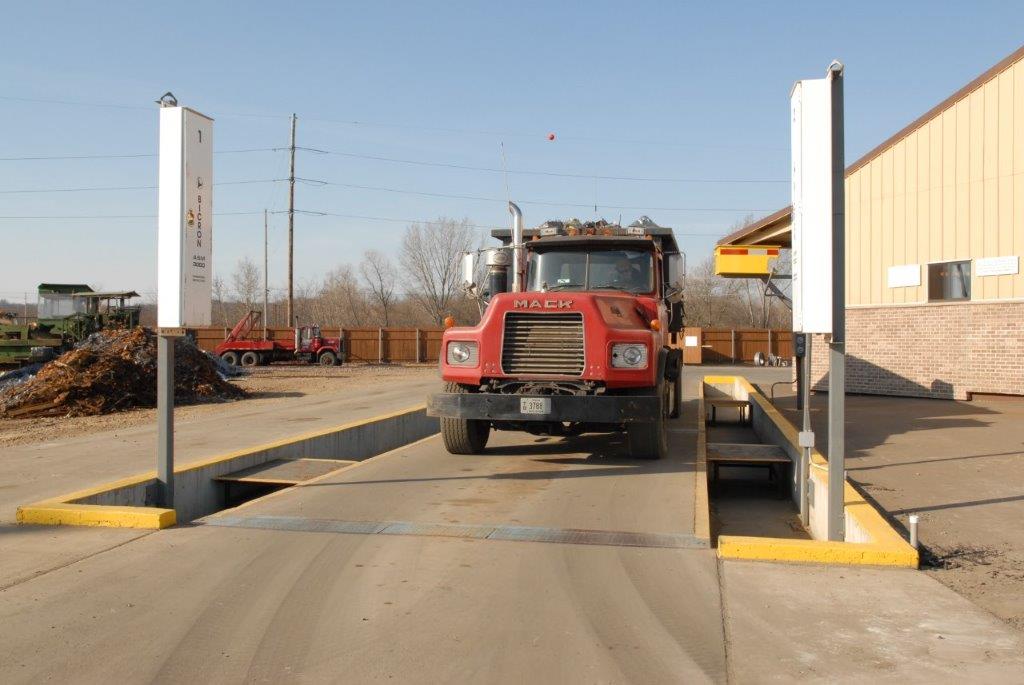
Pictured sometime after 1995, this truck rolls onto a then-newly installed custom-built scale and will next pass between then-newly installed radiation detection devices at the Lorman yard. Radioactive materials were not accepted at the Lorman scrapyard, longtime Loeb family employee Ruth Mack said.
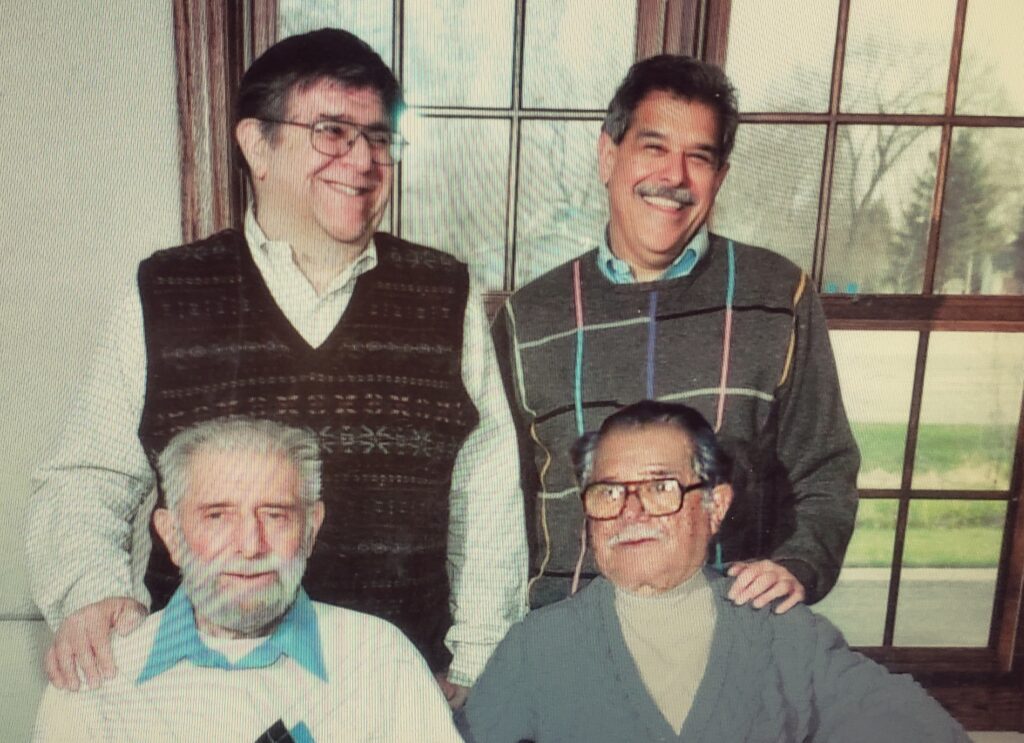
Members of the Loeb family include Neal, back row, at left, and Bruce. Appearing in the front row are Archie, at left, and Bill.
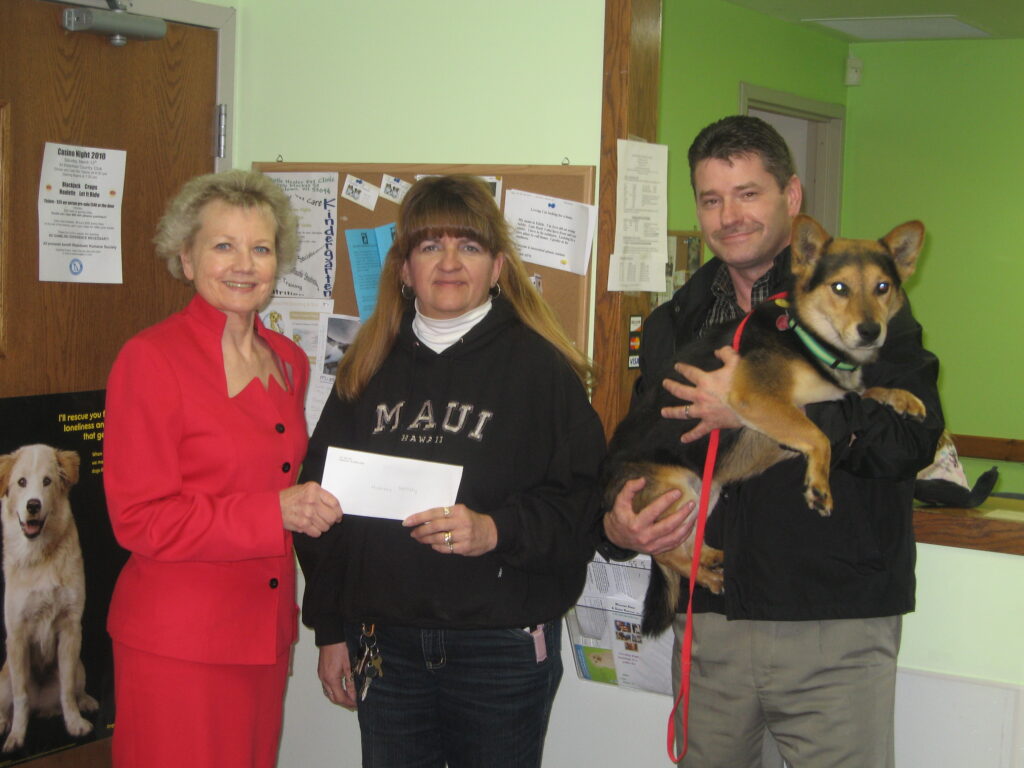
Longtime Loeb family employee Ruth Mack, at left, and Loeb-Lorman Metals employee Jay Schwoch, at right, present the Watertown Humane Society with a donation from the Loeb-Lorman Metals company. The photo was taken in 2010. Pictured receiving the donation is a past-president of the Watertown Humane Society whom employees today were able to identify as “Darlene.”
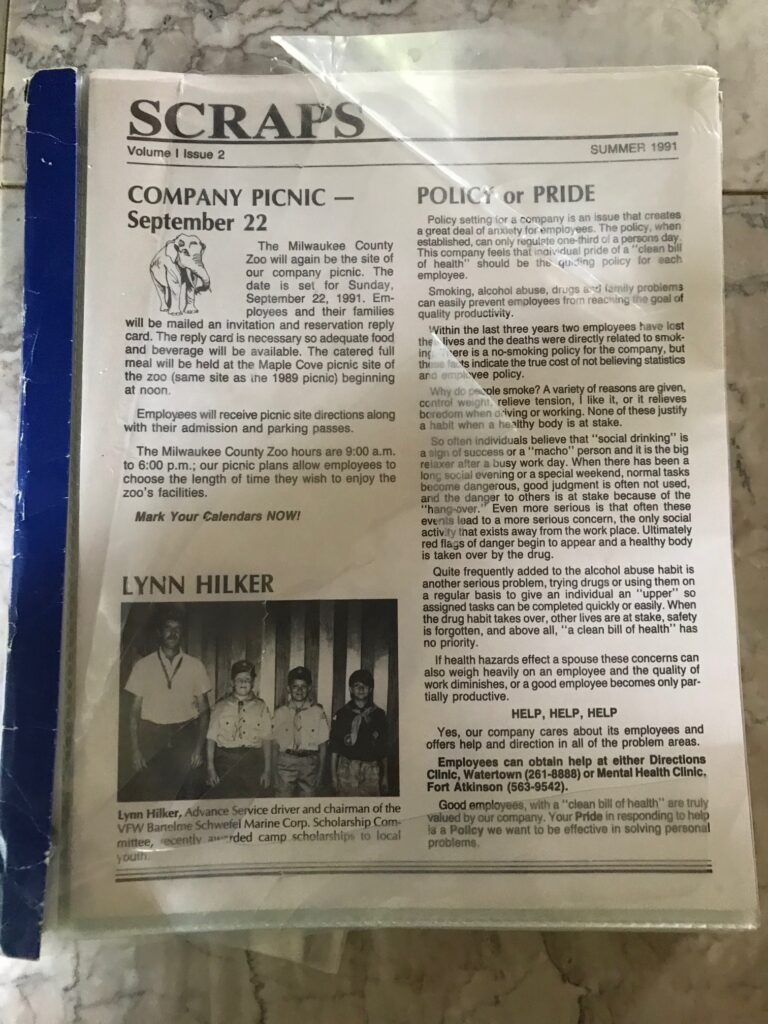
A binder kept by longtime Loeb family employee Ruth Mack documents 24 years of company history between 1991 and 2015. Mack was the editor of the company newsletter called “Scraps,” copies of which are found in the binder.
Kim McDarison photo.
This post has already been read 4986 times!